Adsorption Dryers ( Heatless)
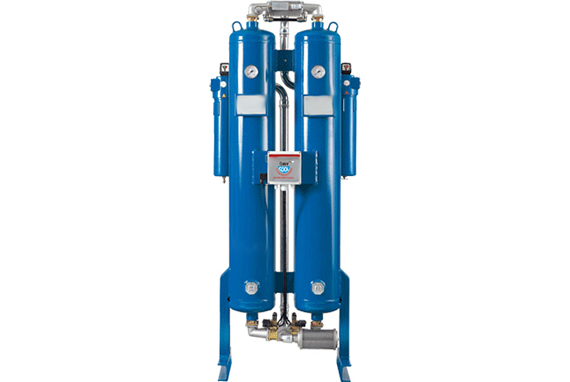
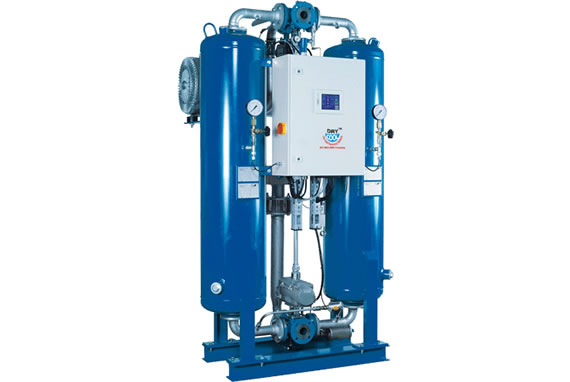
Micro heat regenerated adsorption dryer works in a twin-tower alternative operation mode. Compressed air enters the dryer’s tower A through valve 1A (1B is closed), then is dehydrated and dried under the unique adsorption action of the adsorbent. Finished gas flows to the gas using point through valve 5A (5B is closed); meanwhile about 5% dry air source enters tower B through valve 4B (4A is closed) after being heated by the heater, the adsorbent in which is regenerated after a certain period of heating. Cold blowing begins when heating is stopped, which cools down the adsorption bed in the dryer’s tower B (for use in the next cycle). Finally, the air is discharged into the atmosphere through muffler.
Before switching in the second half period, turn off valve 2B and open valve 1B to equalize the pressure in the two towers (to ensure pressure stability when using the gas and avoid the impact and jitter of the dryer), and the second half period work begins at the same time (the dryer’s tower B works and tower A regenerates). The process is similar to that of the previous half period.
The process is similar to that of the previous half period.
- They save energy besides economising purge by reducing the loss of purge to a minimum of 50%.
- They have controllers with lucid functional displays that are programmable.
- They secure undisturbed operation despite tower changeovers.
- The moisture load is lessened by the auto drain valves in pre and oil filters. Therefore the desiccant life is secured without any extra cost.
- The inclusion of a unique purge economizer in the latest microprocessor based controller which facilitates manual setting up of the dryer load. This device can not only accept up to 3 compressor load/unload contacts but also compute the dryer load dynamically. According to these settings done, the purge can be set. Also, the purge air can be controlled according to the pressure input accepted by the controller.